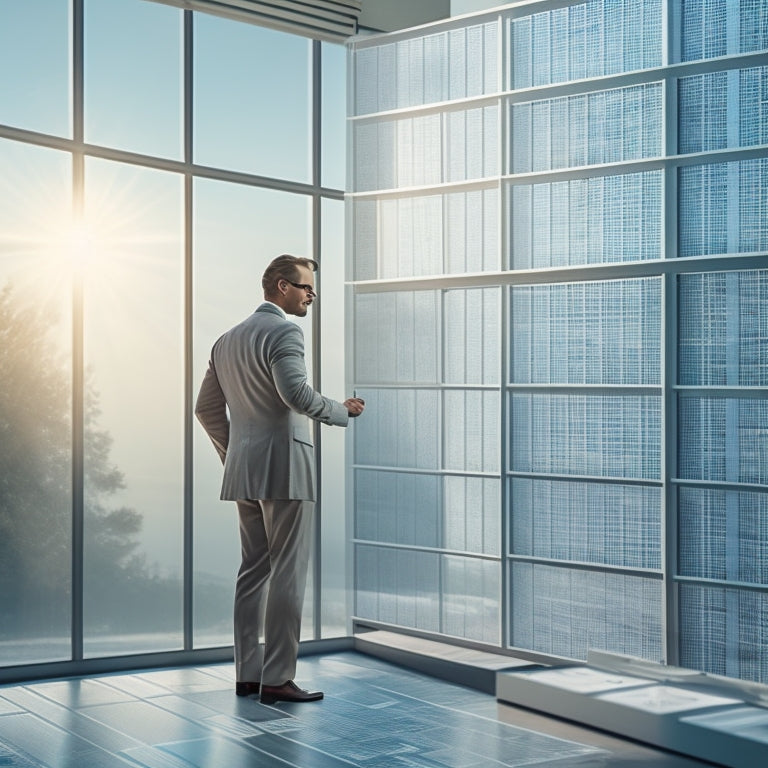
Tracking Mounting System Costs: What to Expect
Share
When tracking mounting system costs, you can expect a breakdown of expenses. For fixed tilt systems, material quality and installation labor costs are key factors. Single axis trackers involve various component costs, while dual axis trackers' prices range from $120 to $250 per megawatt. Racking and mounting hardware costs vary based on material quality and brand reputation. Labor costs depend on project complexity, installer expertise, and regional rates. As you explore the nuances of tracking mounting system costs, you'll uncover more specifics about what drives these expenses and how to effectively plan for your project.
Key Takeaways
• Tracker component costs vary for each part, including actuators, gearboxes, sensors, and motors, impacting overall system cost.
• Installation labor costs range from $15,000 to $40,000 or more, depending on site preparation, foundation work, and system assembly.
• Dual axis trackers can boost energy output by up to 45%, reducing land use and installation costs, with prices ranging from $120 to $250 per megawatt.
• Racking and mounting hardware costs depend on material quality, durability, and brand reputation, with bulk purchasing potentially leading to discounts.
• System design complexity affects overall cost, with more intricate systems requiring more components and labor hours, and balancing complexity and cost is crucial.
Fixed Tilt System Cost Breakdown
Your fixed tilt system cost breakdown typically consists of two primary components: the racking and mounting equipment, and the installation labor costs. These two components make up the majority of your overall system cost.
When creating a fixed budget for your project, it's important to understand the allocation of these costs to optimize your system.
The racking and mounting equipment costs will vary depending on the type and quality of the materials used. High-quality materials may come at a higher upfront cost, but they can provide long-term benefits such as increased durability and reduced maintenance.
On the other hand, installation labor costs will depend on the complexity of the installation, the location, and the installer's expertise.
To ensure system optimization, it's vital to find a balance between these two components. By allocating your fixed budget effectively, you can minimize costs without compromising the performance and longevity of your system.
Single Axis Tracker Cost Analysis
When evaluating single axis tracker costs, you'll want to take into account the component costs, including the tracker's structural and mechanical systems, as well as the photovoltaic panels themselves.
You'll also need to factor in installation labor costs, which can vary depending on the site's terrain and the complexity of the installation.
Tracker Component Costs
The cost of a single-axis tracker's components, including the actuator, gearbox, and sensor, can vary greatly depending on the specific design and material choices. You'll need to take into account the trade-offs between different materials, such as steel, aluminum, or fiber-reinforced polymers, and their impact on overall cost. Additionally, supply chain dynamics, including lead times, shipping, and inventory management, can greatly influence the final cost of these components.
Component | Cost Range |
---|---|
Actuator | $500 - $2,000 |
Gearbox | $1,000 - $5,000 |
Sensor | $200 - $1,000 |
Structural Components | $1,500 - $6,000 |
Motor and Controls | $2,000 - $8,000 |
When selecting materials, you'll need to strike a balance between factors such as strength, corrosion resistance, and weight reduction against cost. By understanding the cost drivers of each component, you can make informed decisions that optimize your tracker's performance while keeping costs in check.
Installation Labor Costs
Labor costs for single-axis tracker installation can add up quickly. Factors like site preparation, foundation work, and system assembly contribute to a total that can range from $15,000 to $40,000 or more, depending on the project's complexity. When planning installation, it's crucial to consider the labor costs associated with getting the tracker up and running.
One key factor influencing labor costs is the local workforce demographics. Areas with high labor union participation may have higher costs due to union rates and benefits. Regions with a shortage of skilled workers may also drive up costs as contractors compete for talent.
To better understand labor costs, research local labor unions, prevailing wages, and benefits in your area. Understanding these factors helps estimate labor costs accurately. This allows for better budget planning for your single-axis tracker installation. Managing the project's bottom line ensures successful installation.
Dual Axis Tracker Cost Comparison
Comparing dual axis tracker costs reveals significant differences between manufacturers, with prices ranging from $120 to $250 per megawatt, depending on the specific system design and installation requirements. As you evaluate dual axis tracker options, take into account the efficiency gains and cost savings each system can provide.
When appraising the cost-effectiveness of a dual axis tracker, you'll want to contemplate the increased energy production it can provide. A high-efficiency dual axis tracker can boost your energy output by up to 45% compared to fixed-tilt systems. This heightened energy production translates to higher revenue and faster returns on investment.
Moreover, dual axis trackers can also reduce land use and installation costs. By maximizing energy production per acre, you can reduce the overall project size, resulting in lower land acquisition and preparation costs. Additionally, dual axis trackers can be designed with fewer foundations and less material, leading to further cost savings.
As you weigh the costs and benefits of different dual axis tracker systems, be sure to take these key factors into account to make sure you're getting the best value for your investment.
Racking and Mounting Hardware Costs
When evaluating the costs of your tracking mounting system, you'll need to take into account the expenses associated with racking and mounting hardware. These costs can add up quickly, depending on the complexity of your system design.
You'll want to carefully assess the prices of individual hardware components, such as clamps, rails, and bolts, to get an accurate estimate of your total costs.
Hardware Component Costs
Your racking and mounting hardware costs will depend on the specific components you choose, which can include clamps, trackers, and roof attachments. These components can vary considerably in price, depending on factors such as material quality, durability, and brand reputation.
When it comes to hardware component costs, several factors can influence the final price tag. Consider the following:
-
Material sourcing: The cost of materials, such as aluminum or stainless steel, can fluctuate based on market demand and supply chain dynamics.
-
Component complexity: More complex components, such as trackers or adjustable clamps, tend to be pricier than simpler components like roof attachments.
-
Brand reputation: Components from well-established brands may come with a higher price tag due to their reputation for quality and reliability.
- Quantity and bulk purchasing: Purchasing larger quantities of components can lead to discounts and lower overall costs.
System Design Complexity
Your racking and mounting system's design complexity greatly influences its overall cost, as a more intricate system requires more components and labor hours. As you plan your system, you'll need to contemplate the complexity metrics that will impact your bottom line.
Design Complexity | Impact on Cost | Design Tradeoffs |
---|---|---|
Simple | Low | Limited customization options |
Moderate | Medium | Balance between cost and customization |
Complex | High | High customization, but higher cost and labor hours |
When evaluating design complexity, take into account the number of components, installation time, and labor requirements. A more complex system may offer greater customization, but it will also increase costs. You'll need to assess the benefits of a customized system against the added expense. By understanding the impact of design complexity on your mounting system's cost, you can make informed decisions about your design tradeoffs. By striking a balance between complexity and cost, you can create an efficient and cost-effective system that meets your needs.
Installation Labor Cost Factors
Labor costs associated with installation can add up quickly, depending on the complexity of the project and the installer's level of expertise. As you plan your mounting system installation, it's important to take into account the labor cost factors that will impact your overall expenses.
When evaluating labor costs, you should take into account the following factors:
-
Workforce dynamics: The size and experience of the installation team will greatly affect labor costs. A larger, more experienced team may complete the project faster, but at a higher cost per hour.
-
Labor laws: Adhering to labor laws, such as overtime pay and worker's compensation, will contribute to your labor costs.
-
Regional labor rates: Labor rates vary by region, so it's crucial to research the going rate in your area.
- Project complexity: The complexity of your project will impact labor costs, as more intricate installations require more time and expertise.
System Design and Engineering Fees
System design and engineering fees, which can account for a significant portion of your mounting system costs, are influenced by the complexity of your project's design and the expertise of the engineers involved. As you plan your project, it's important to take into account the impact of design complexity on these fees.
Projects with unique or custom designs will likely require more engineering hours, increasing costs. Conversely, standard or modular designs may reduce engineering time and fees.
Your project timelines also play a vital role in determining these costs. Tight project timelines can lead to rushed design iterations, resulting in additional engineering hours and higher fees. On the other hand, allowing for a more relaxed project schedule can facilitate more efficient design iterations, reducing engineering time and costs.
When working with engineers, it's crucial to discuss and agree upon project timelines and design iterations to make sure you're getting the best value for your investment. By understanding these factors, you can better anticipate and manage your system design and engineering fees, ensuring a more cost-effective mounting system.
Ongoing Maintenance Cost Considerations
Regular inspections and routine maintenance are crucial to extending the lifespan of your mounting system, and understanding the associated costs is essential to creating a thorough budget. As you plan for ongoing maintenance, consider the following factors that can impact your costs:
-
Power consumption: Your system's power consumption can affect your energy bills and overall operating costs. Be sure to factor in these expenses when budgeting for maintenance.
-
Inverter replacements: Inverters are critical components that require periodic replacement. Budgeting for these replacements can help prevent unexpected expenses.
-
Scheduled maintenance: Regular maintenance can help prevent unexpected downtime and reduce repair costs.
- Repair and replacement parts: Having a stock of spare parts on hand can help reduce downtime and minimize repair costs.
Frequently Asked Questions
How Do I Ensure My Tracking System Complies With Local Building Codes?
To guarantee your tracking system complies with local building codes, you'll need to research and obtain necessary permits, paying associated fees, and verify that your system meets code requirements to avoid costly rework or fines.
Can I Integrate My Tracking System With Existing Roofing Infrastructure?
You can integrate your tracking system with existing roofing infrastructure, but make sure the structural integrity of the roof isn't compromised, and be prepared to overcome installation challenges, such as obstructions or uneven surfaces.
What Are the Benefits of Using a Single Manufacturer for All Components?
By choosing a single manufacturer for all components, you'll simplify warranty management, streamline your supply chain, and reduce logistical headaches, ultimately saving you time and resources.
How Does System Design Impact the Overall Cost of My Tracking System?
When designing your tracking system, you'll find that component selection and structural integrity greatly impact overall cost, as best choices can reduce material usage, simplify installation, and enhance durability, ultimately saving you money.
Are There Any Incentives for Using Eco-Friendly Tracking System Materials?
You can benefit from tax credits and government grants when using eco-friendly tracking system materials, incentivizing sustainable practices and reducing your project's overall cost, making environmentally responsible choices a smart business decision.
Related Posts
-
Is Switching to Green Energy Solutions Easy
Switching to green energy solutions isn't just easy; it's also beneficial. You can greatly cut utility costs and enjo...
-
Top 10 Off Grid Camping Gear Must-Haves
When you're off-grid camping, the right gear is crucial for a smooth expedition. Start with a durable, weather-resist...
-
Top Camping Water Bottles for Adventure
When you're out adventuring, picking the right camping water bottle is essential for staying hydrated. Look for durab...